谈到水厂自控系统的设计就不得不谈到智慧水务叶圣炯的《水厂沉淀池吸泥桁车的自控改造》这篇论文。这篇论文以水厂沉淀池吸泥桁车为例谈了自控系统的设计思路和程序实现。水厂的其他自控系统也可以根据这个思路实现。具有很强的借鉴意义。以下就是这篇论文。
水厂沉淀池吸泥桁车的自控改造
叶圣炯,王蕾
摘要:
自动控制系统已经成为当今水厂生产运行中的核心。因此利用现有的资源对一些尚未自动化的老系统进行自控改造十分必要。利用PLC对某水厂的平流式沉淀池吸泥桁车进行自动化改造,从对自控方案的设计、三种方案的选择,自控系统流程功能的分析和设计,PLC程序的实现与调试三个方面来对该工程进行分析研究。实现了吸泥桁车开停联动的自动化、多线路运行路径的优化、循环定时启动等功能,解决了原系统操作复杂、水量浪费大、效率低下等问题,提高了生产效益,降低了管理成本。
关键词:
自动控制;PLC;吸泥桁车;
1、 引言
自动化控制在水厂的日常生产中已经越来越重要了,因而近年来新建设的水厂中自动化系统的运用已经成了标配和主流。自控系统的运用对于水厂来说在提高生产效益,降低管理成本方面十分有效。但是在一些上个世纪建造的老水厂中,自动化的运用还不很普遍,手动控制仍然是主流。所以,如果利用有限的资源对一些老系统设备进行自动化改造具有十分重要的意义。
以南方某水厂为例,该水厂有一套日处理能力为15万吨的净水处理系统,水源为苕溪水系,该系统建设于上个世纪八十年代,在生产系统上仍然以手动控制为主。采用加药、混凝、沉淀、过滤的常规工艺。
在常规处理工艺中,沉淀这一环节承接了混凝和过滤两个环节。其重要原理是水中悬浮颗粒依靠重力作用,从水中分离出来的过程称为沉淀。颗粒比重大于l 时,表现为下沉;小于1 时,表现为上浮。其作用为原水经投药、混合与絮凝后,水中悬浮杂质已经形成粗大的絮凝体,要在沉淀池中分离出来完成水质的澄清。
在沉淀池的选择上该系统采用了平流式沉淀池,平流式沉淀池为矩形水池,上部为沉淀区,下部为污泥区,池前部有进水区,池子后部有出水区。在实际运行过程中水厂要靠吸泥桁车利用虹吸的原理来对下部的污泥区进行排泥。
原有的吸泥桁车在操作上采用人工手动操作,需要人工按步骤完成建立真空,启动潜水泵,控制桁车行程排泥,介绍后停泵破坏真空等一系列环节,操作比较繁琐,过程中各个时间点要靠个人经验估计。同时不合理的行程造成了水量的浪费。为了提高工作效率,降低生产成本,在现有基础上对吸泥桁车进行自控改造已经是迫在眉睫。
2、 自控方案设计
从经济角度考虑,在设计中遵循了尽可能减少改动环节,降低改造成本的原则。
一般的自控系统分为上位机和下位机两个部分。下位机一般由PLC及相关电器柜组成,负责实地的控制运行;上位机一般由组态软件及计算机组成,负责上层的监视和控制。故在最初的方案设计时按照常规,
采用了上位机+下位机的方案。
但是考虑到该水厂并无全厂DCS系统的现实情况,作为一个简单独立的系统为其配置单独的上位机似乎意义不大。
因为上位机具有三种功能:
第一是远程控制桁车,即在控制室操作按键来控制桁车的运行。
第二是监视桁车运行,即在电脑画面上监视桁车运行。
第三是桁车运行组合编程。
该厂桁车操作工办公室距离桁车只有几步路,远程控制和监视意义不大,其在办公室门口即可看到实体的桁车运行。运程控制在自控系统中只是辅助操作,充其量只能算半自动。将上位机功能集成在现场操作箱上同样可以实现而且实用。上位机的唯一优势是运行组合编程,涉及复杂的操作,上位机比较占有优势。但组建上位机还需涉及无线通讯和控制台计算机,组态软件购置等成本,故决定将运行组合编程模式集成在现场操作箱上以实现低成本目标。所以上位机+下位机的结构模式被排除。
第二种方案是下位机+触摸屏结构模式。
相比第一种模式,在现场的操作箱上设置触摸屏,即将第一种模式中的上位机减去无线通讯的方式,将上位机搬到了操作箱上,也就是说把上位机从控制室换到了桁车操作箱现场,同样需要承担上位机的相关成本,考虑到触摸屏的价格该方案排除。
第三种是方案是下位机实地操作的结构模式。
即去掉了上位机部分,砍掉了花哨的功能设置。吸泥桁车的核心功能是自动运行,只靠下位机系统即可实现。而半自动方面的功能,通过操作箱按键来实现。这种设计即满足了功能需求又节约了成本,符合实际需求,故采用此方案作为吸泥桁车系统的结构模式。
3、 功能设计
吸泥桁车在运行过程中涉及吸泥桁车的开停联动、运行路径、开停判断等三项功能,具体功能流程见图1.
在吸泥桁车的开停联动功能中关键是真空的建立和破坏以及潜水泵的开、停。在原先的手动操作中需要通过一定的顺序点按钮来实现,在自控状态下,这个步骤由程序一步到位自动完成。
基本的过程是系统获取启动信号发指令启动潜水泵,潜水泵运行一段时间后判断真空是否形成。实际过程中可采取形成真空接触点或根据时间延迟来判断真空形成。系统收到真空形成信号后发指令启动电机开始运行。反之则实现停止功能。
在吸泥桁车运行路径的设计中,采用了全行程、半行程和三分之一行程相结合的方式。
由于受供水旺季淡季以及原水水质变化的影响,沉淀池污泥积累的速度是不一样的,如果用同一种模式运行必定会造成排泥量不足影响运行效率或是排水过量的造成浪费的局面,因此,设计多种行程方式,根据实际特点进行合理的选择是最适宜的方法。
由于成本考虑,并没有把原吸泥桁车的匀速电机改成变频电机,因此桁车的运行过程中一直是匀速的,可以用时间来控制桁车的运行路径。
基本的过程是设定全程运行时间为T,桁车在首次运行时会进行判断是否处于起点,如果不是则会返回起点开始运行,运行至1/8T时会在沉淀池头部1/4处来回运行一次,这是因为在生产实际中,沉淀池头部往往积累着更多的污泥,需要来回清理。
在完成头部清理后继续前进,再运行1/2T到达沉淀池尾部。头尾部设置到达反馈信号,反馈信号优先级高于时间控制。在尾部停留一定的延迟时间后返回,完成全程运行。半行程、三分之一行程过程类似。
开停判断功能由于根据水质自动判断的技术不成熟,采用时间判断的方式。在供水淡季,原水水质情况较好的情况下采用24小时定时三分之一行程的方式,在供水旺季,原水水质较差的情况下采用24小时定时半行程的方式,如遇水质特别差的极端天气启用24小时全行程的方式。由PLC的定时器进行计时控制。
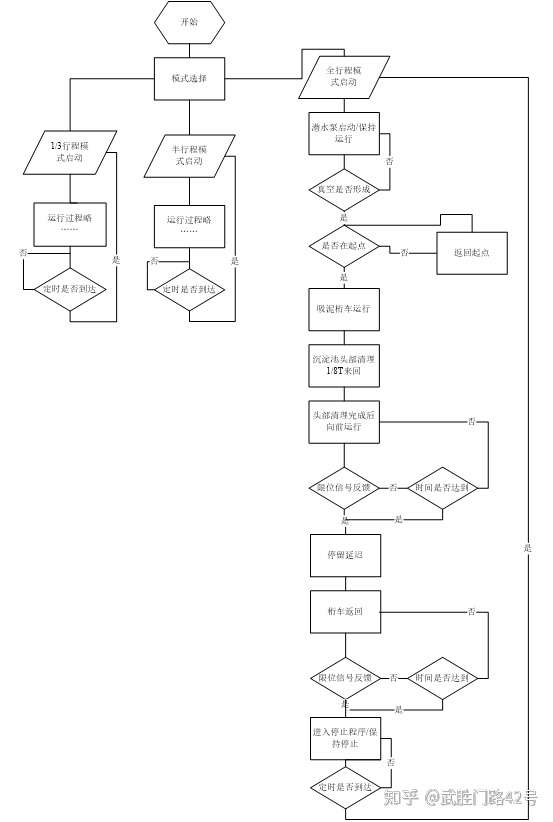
4、 程序实现
整个吸泥桁车的自控改造过程中最关键的就是可编程控制器PLC的运用。PLC是整个自控系统的核心。PLC我们采用的是1761L20BWB系列,该PLC集成了电源、CPU和输出输入模块,属于微型PLC系列。之所以采用该系列PLC主要是看中其集成、小型、功能全面等特点。
该PLC与操作柜均设置在吸泥桁车上,在现场进行控制。
该款PLC的编程平台是RSlogix500,在编程语言上采用了工程领域主流的梯形图方式进行程序编制。
在程序结构上,采用了主程序与子程序相结合,按需调用的方式。该系统由一个主程序和五个子程序构成。其中主程序主要负责桁车主流程,根据需要调用各个子流程。子程序包括桁车联动开停程序、全行程排泥子程序、半行程排泥子程序、1/3行程排泥子程序、安全子程序。各子程序负责各自的流程,其中安全子程序主要负责系统启动前的自检、报警信号的处理、紧急情况复位等系统运行过程中的安全问题。
在程序调用上严格遵循调用唯一性的原则,利用多条件判断来控制子程序调用的唯一性。图2即为在主程序状态下调用三个子程序的梯形图语句。
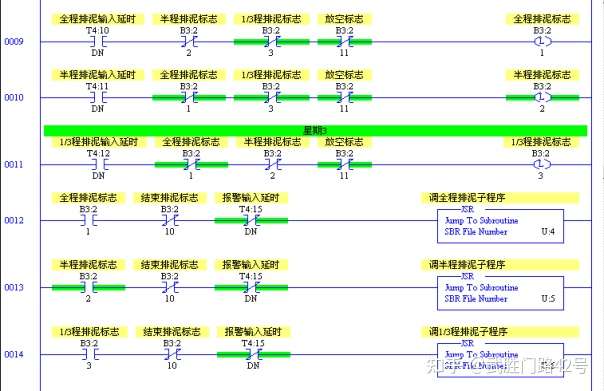
为提高调试效率,在实际过程中采用功能调试和现场调试相结合的方式来进行程序调试。
功能调试即将PLC上电,灌制程序,不接任何输出输入点。桁车的反馈信号点均由人工来模拟,以此测试这个程序的功能是否可以实现。在时间控制上将间隔和运行时间模式缩小,比如将2小时缩小至2分钟等。主要是观测程序是否存在冲突,功能是否完备。
现场调试是在功能调试成功的基础上进行的。进行功能调试有助于现场调试的成功率。现场调试则是完全模拟现场运行状况,进行实景的运行测试。
5、结束语
该系统改造后运行稳定,效益明显。由工作量的变少变精带来了管理成本的下降和生产效率的提升,由控制优化带来了生产成本的下降,其中试运行当月水厂自用水率下降了1%,同时也因为提高了沉淀池的运行效率而间接的降低了加药量。所以,对老系统进行自控改造是一条提升老厂生产效率切实可行的道路。