在《水厂加矾系统的SCD反馈控制的研究 》一文中,我们得知如果要使用PID+SCD的模型还需要解决一个关键问题,那就是由于水质变化快而带来的反馈滞后性问题。
原水从加药到沉淀池出来后,中间的时间很长,例如我们在设计的时候得到的平均时间是2个小时以上,也就是说SCD反馈回来的沉淀池后浊度数据已经是2个小时后的数据,如果原水水质在2个小时内发生很大的变化时,那么这个反馈数据已经无法指导即时的投加量,并且会出现误判,从而导致系统错误。这就是我们所说的反馈滞后性问题。
由于质突变是常态存在的,变化周期往往都很短。这也是导致很多运行加矾自动化系统的水厂开始时运行情况良好,但时间一长往往就出现了各种问题,这是因为随着时间的积累,水质变化频繁的情况出现次数增加,从而增加了系统判断失误的次数。
而系统的使用者就将此归结为系统设计有问题而放弃使用,最常见的情况就是出现半人工半自动的方式来操作各类加药系统。水质稳定时使用自动运行,变化快时人工判断。
我们在设计时对PID+SCD的模型进行了改进,针对滞后的问题,我们经过反复研究和同类系统比较,决定在模型设计中加入了两个因素予以校正。
第一个因素是模拟人工。
因为在实际使用中我们会用人工判断代替自动运行来解决判断失误的问题。那么我们设计模型时要解决同样的问题也可以采取相似的手段。
建立一个模拟人工智能的计算中心来代替人工判断。由于操作员工往往是在利用自己的经验而采取判断的,因此这个人工智能计算中心是一个建立在经验库基础上的判断中心。
我们在中央处理单元决定设计一个专家知识经验库,利用经验数据来自动判定数据的趋势和走向。这个专家知识经验库实际上是一个历史数据库加上一个判断程序,而这个历史数据库是基础。专家知识经验库的核心运算方法如图所示。
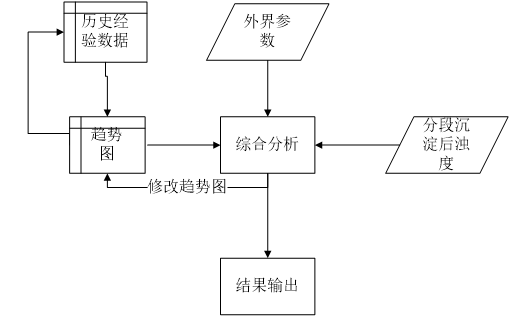
为了获取经验数据,在设计投加药系统之前必须获得该水源地两年内的水质变化情况数据,如果是新建水厂,那至少要做半年以上的中型实验以获取一定的可靠数据。数据的数量是趋势图可靠性的保证。
第二个因素是减少滞后时间
实际上滞后时间越长判断的失误率就越高。在建立专家知识经验库的基础上,为了使这个经验库判断的更为准确,我们就要采取一些辅助措施来减少滞后的时间。我们可以采取分段取样的方法,在沉淀池的中间采点取样。
例如整个沉淀过程是2个小时,我们要在2个小时之后才能取得沉淀后的数据,如果我们在沉淀进行到一半的时候进行取样,就可以减少一半的滞后时间。因此合理增加取样点是解决滞后问题的一个有效措施。